Hose Asset Management for Flexible Assemblies
As a company, Flextech’s aim is to pioneer hose assembly innovation and hose asset management solutions for food, beverage, pharmaceutical & life sciences, chemical and defence markets through responsibly maintained hose registers for the businesses we support.
Increase hose lifespan through Asset Management, Hose Inspections, On-site Testing & more.
Hose Health Check
In order to fulfil our aim, we developed The ‘Hose Health Check’, a series of hose checking, guidance and maintenance systems designed to be developed into a full hose asset management system once initial checks have been done and need established/communicated to the company we’re supporting.
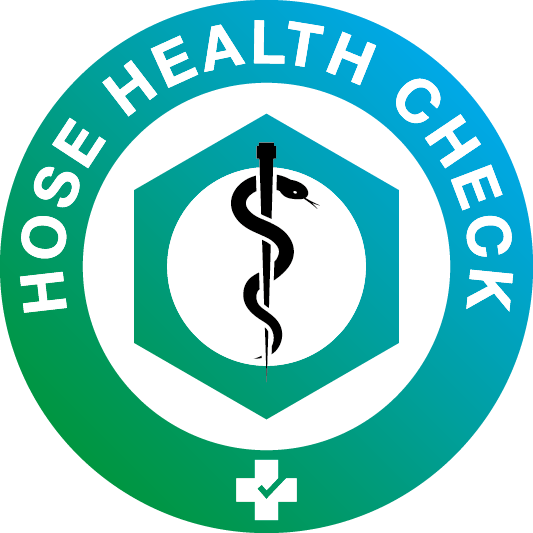
On-Line Hose Register - Asset Management
The NEW FHS On-Line Hose Register Asset Management software developed
by Flextech is the easy way to keep track of your hose assemblies
ensuring they meet your inspection, maintenance quality and health &
safety plan.
Take full control or work with the Flextech Team who can help you
register all your site hoses, annual inspections and hose testing
requirements. Print your own asset reports to show evidence you are
compliant in maintaining your assets.
Click here to log in. On-Line Register
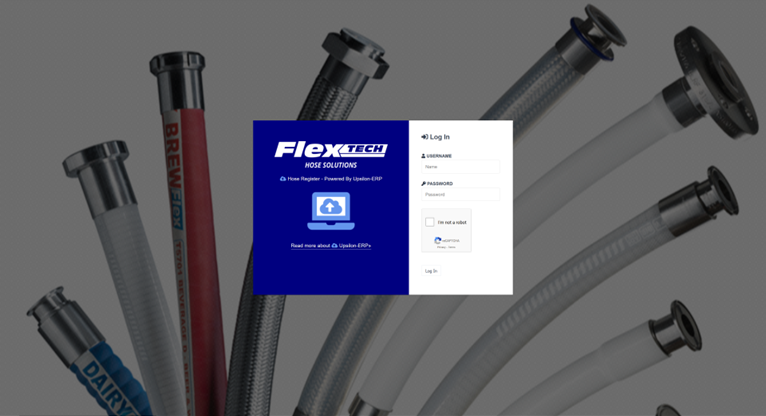
Hose Surveys
At this stage we begin to list all the hoses used and to then be entered into a spreadsheet. There is a wide variety of details that we collate about each hose in order to understand the hose in it’s entirety.
Where necessary we enter any observations we have made accompanied by our recommendations made from our visually inspection for any signs of damage or loss of integrity on the hoses. The aim of this procedure is to give you a very clear and up-to-date health status of your hose assemblies.
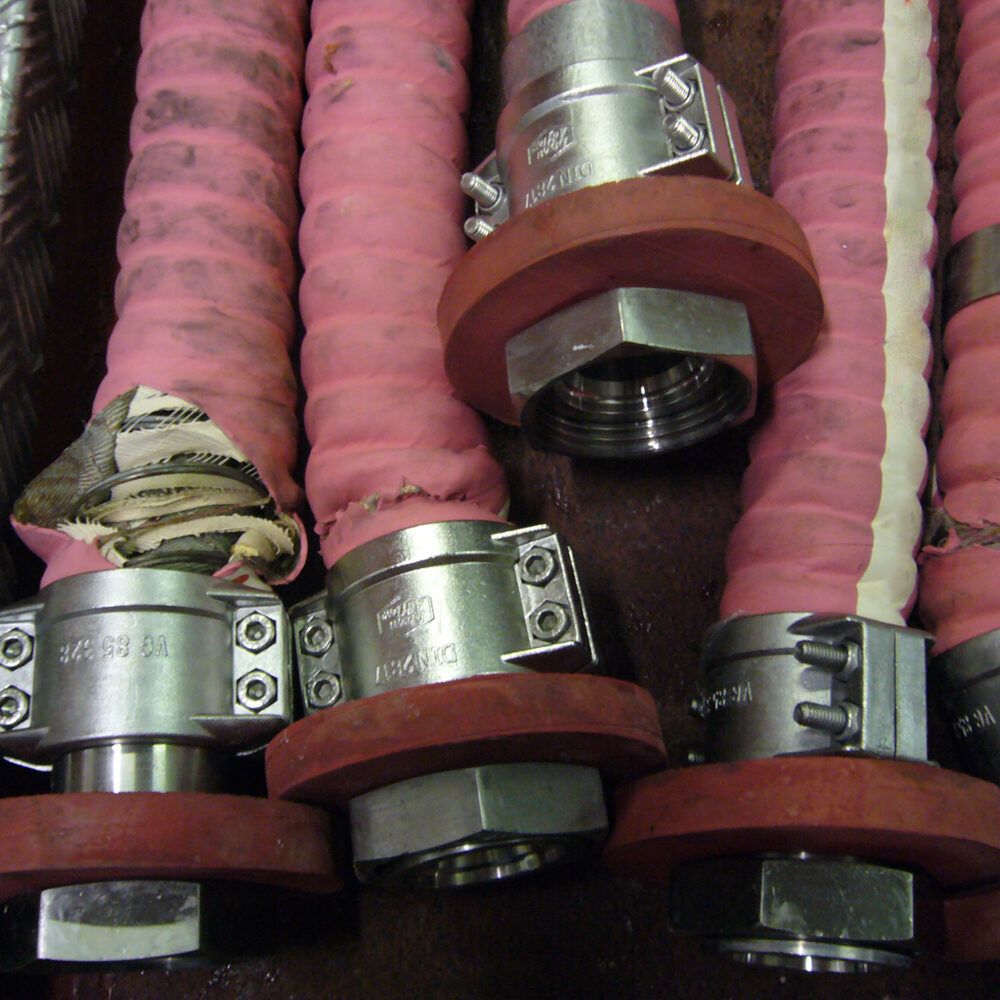
The Registering of Assets
If hose assemblies already have asset numbers allocated to them, these are taken note of. If asset numbers do not exist, we will work with our clients to devise a suitable numbering method and agree on the best approach and tag type to clearly identify the hoses.
All references are submitted against the corresponding hose within the register. Tagging Solutions are available for hose assemblies and can be agreed by both parties prior to commencing this activity.
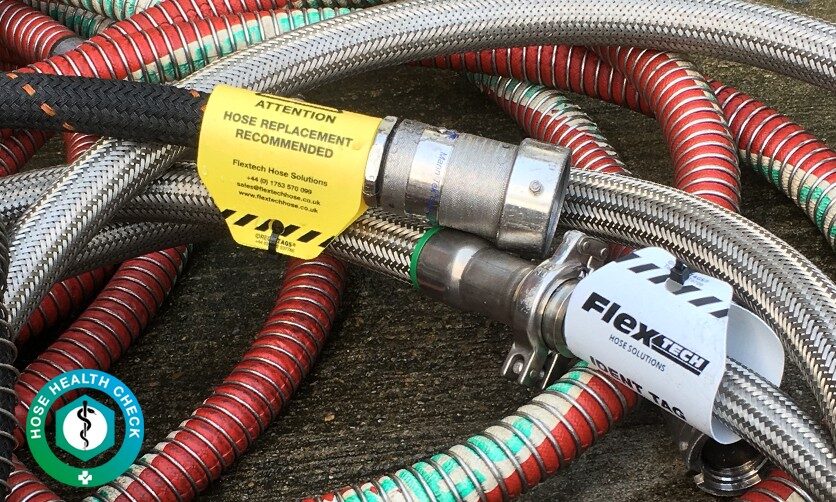
On-site Hose Testing
Truthfully, this is the only true way to eliminate any impending risk. Hoses nearly always fail from the inside out and so they only way to establish an impending failure is to expect them from an internal perspective. The process is relatively simplistic and will follow the guidelines listed:
- Visual Inspection – Here we are looking for anything that compromises the integrity of the hose such as; crack, bubbles, kinks, corrosion of wires, and/or end fittings and severe impact to the hoses.
- Electrical Continuity Test (If Required) – Ordinarily looking to achieve less than 1Ω per metre
- Non-destructive Hydro-static Testing – Ordinarily to 1.5 times the working pressure of the application.
- Non-destructive Nitrogen Testing – Used instead where water cannot be used for testing purposes
- Additional Electrical Continuity Test – Once pressure testing is completed we will check the electrical continuity of the hose again, to ensure there has been no damage to inner or outer wires.
- Tagging – Once a hose has been passed as fit for purpose we will apply a coloured strap that will be inline the IMO colour coding standard. Asset tags can be applied at this stage too if required. Any hoses which are failed will be tagged accordingly and bought to your attention.
Programme of Events
The most crucial part is to ensure that there is an agreed programme in place to eliminate any issues in the future. Therefore we strongly recommend the following actions are agreed upon:
- Regular meetings to ensure that the processes put in place are working. If not we can instigate corrective actions
- Agreed programme to carry on the visual inspections
- Agreed programme for on-site testing
Additional Services
To help lower the risk profile associated with flexible hoses, we offer on-site hose training that will help operatives to be able to spot signs of premature failure of the hose. In addition we can educate operatives into the correct installation of hoses and how to handle hoses correctly.
In Summary
The advantages of having your hoses tagged and entered onto a data base are clear for all to see. Auditing becomes very straight forward and should urgent replacement become necessary for any reason the date when the hose in question was last inspected, manufactured, installed and pressure tested is clearly visible. In addition to this if a hose should fail you can easily order an urgent replacement by quoting the unique hose tag number.
This system, if implemented may also be used to monitor specific areas for downtime or loss of production time due to machine failure. For example if a hose is continuously failing in a specific area then further investigation can be pursued to check whether the cause is a hose or application issue, machine issue or simply that the operator in this area may require further training in how to use and fit hoses. At the end of each year the hose purchases for every area together with associated downtime and lost production time may be reviewed and the results addressed accordingly.
In order to maintain optimum efficiency Flextech would also suggest that a quarterly visual inspection of your hoses is carried out either by a Flextech representative or a trained customers employee (full training will be given).